導入の目的
業務用エアコンの室外機の製造ラインで、 冷媒封入作業者のミスによる不良発生を防止する !
三菱電機株式会社の静岡製作所では、新たな冷媒の製品を追加生産するにあたり、RFIDを活用した生産機種ごとの自動管理システムにSA1を導入しました。
事例のポイント
- 製品に取り付けた電子タグのID情報を自動で読み取り、1台ごとに封入量の指示をGOTに表示させることで、作業者のミスを防止。
- 封入したガス量等の実績データをGOTに表示させることで、適切かつ確実なガス封入を実現。
- SA1-Ⅲ※(設備監視)によって、ガス封入作業後の実績データを上位データベースに登録することで、バックアップを兼ねた二重管理を実現。
- 「トレーサビリティ」の実現により、機種ごとの市場対応や原因特定のスピード化など、品質保証の精度が飛躍的に向上。
※三菱電機システムサービス株式会社製監視制御システム
世界市場向けの小ロット多サイクル生産ラインに
三菱電機静岡製作所は1954年、主に家庭用冷蔵庫やエアコンの開発と製造を目的に設立。以来、時代のニーズを先取りした機能やユーザビリティの追求によって、画期的な新製品を次々に生み出してきた。現在も“Eco Amenity”を開発理念に掲げ、最先端の熱解析、気流解析、インバータ制御など先端的な技術を駆使した高機能かつ高品質の製品開発を押し進めている。
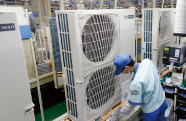
世界市場に対応したPAC室外機製造ライン。多いときには1日に60機種が1つのラインを流れる「小ロット多サイクル生産」を行っている。
そんな静岡製作所で1年ほど前、業務用のパッケージエアコン(以下、PAC)に、新たな冷媒ガスR32を使用した新製品開発の話が持ち上がった。R32は現行のR410aに比べ地球温暖化係数が約1/3と小さく、環境性能の向上に適している。しかし、R32はわずかに燃性を持つ。製品の安全性に問題はないが、その使用が認められていない国も存在する。グローバル市場を相手にしている静岡製作所では、すべての製品の冷媒を一律に切り替えるわけにはいかなかった。また、機種数が多いPAC製造では、短納期を目的に製品のプラットフォーム化が図られ、お客様のご要望に応じてその時に必要な商品を製造できる「小ロット多サイクル生産」を実施。つまり、同一ラインで、多いときには1日に60機種もの製品が作り出されている。そこに、異なる冷媒の製品がロットごとにバラバラに流れていくことになる。 「冷媒の違いは、製品を外から見ただけでは全く分りません。それでも絶対に間違いを起こさず、しかもコストをかけずに生産する方法を考えるというのが、私たちに与えられた課題でした」(石橋氏)
第一の課題は混合生産におけるポカヨケ
従来の製造工程ではロットごとの管理が基本だった。冷媒封入の作業者はまず、ロットの先頭で「組立カード」のバーコードを読み込む。その記録がパソコンに送られ、ネットワークで繋がったサーバ内の情報と照合し、必要な作業指示が現場のモニタに映し出される。そして、次のロットに切り替わるまで封入作業を繰り返す。作業者に頼った運営システムでは新たな冷媒を採用する商品の量産化に対して懸念があった。
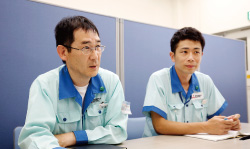
システム導入を主導した三菱電機静岡製作所パッケージエアコン生産管理課の石橋章佳氏(左)と都築祐一氏(右)。
そこで2つの解決策を選んだ。1つは、製品側のガス封入口の形状と製造側のガス封入ノズルの形状を冷媒ごとに変えるというハード的な対策。 もう1つは、ソフトウェアによって1台1台個別に管理する方法だ。「狙いは、混合生産におけるポカヨケです。それだけなら、ハード的な対策で良かったのかもしれません。しかし、工場の中の多種多様なシステムの老朽化対策や統合の必要性、さらに今後の自動化なども展望すると、これからはソフトウェアで管理していくべきだというのが結論でした。その先駆けとなるシステムの構築をめざそう。これがRFIDシステムを導入のきっかけになりました」(都築氏)
新製品投入を機にソフトウェアによる自動管理へ
RFIDを使った新しいシステムでは、製品1台1台に電子タグを取り付け、機種ごとの管理に切り替えた。これにより、封入すべき冷媒量の指示を個別に行うことができる。さらに、実際に封入したガス量や、その前工程で製品内を真空にした際の真空度などの実績を現場に設置したGOTに表示。作業者はそれを確認しながら操作できるようになり、適切かつ確実なガス封入を実現した。
また、これまでは、バーコードを読み込む際に初品チェックシートをロット内の製品に貼り付けることで作業者の「見逃し」を防いでいたが、こうした作業手間も、電子タグで自動化することで削減することができた。
「これまで人に頼っていた部分を自動化し、コンピュータ管理することで、不適合品が下工程に流出するリスクを低減できたことだけでも充分な効果だったと思います。さらに、作業者が封入したガス量などの実績をリアルタイムに確認できるようになりました。この『見える化』によって作業性も格段に向上しました」(都築氏)
では、RFIDシステムの導入にあたって、苦労されたことは?「電子タグの情報を読み取れる距離と正確さは、既存の製造ラインに適応させる上では重要でした。当初、アンテナやセンサーをどう配置するかで苦労しましたが、機器の特性を理解することでラインの変更を最小限に留めることができました」(都築氏)
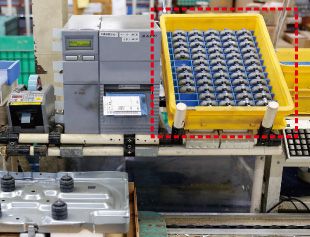
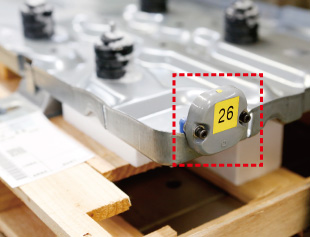
そのタグをこれから製造ラインに乗せる製品1台ごとに取り付けていく。
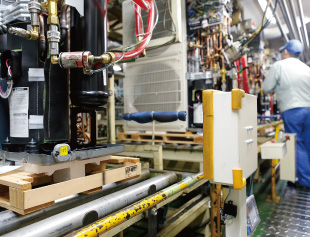
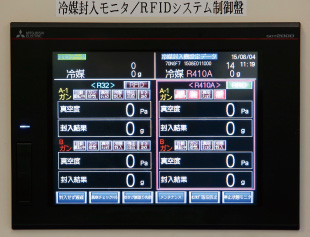
トレーサビリティによって品質保証の精度が向上
機種ごとの管理への切り替えは、さらなるメリットをもたらした。新たなシステムは、封入したガス量と事前の真空度、それが基準値に対してどの程度振れバラツキがあるのかまで1台1台詳細に記録する。これにより万が一、マーケットから品質に対する問い合わせがあった場合にも、1台ごとの履歴を提示できるようになった。また、急にラインが停止してしまった場合にも、どこからどこまでの製品に支障が出るか、正確かつスピーディに特定することもできる。
さらにSA1-Ⅲは、現場で収集したデータを上位のホストサーバへ送ることができるため、事務所のパソコンからでも現場の状況を即座に判断できるようになった。原因解明にいたる時間が圧倒的に早ければ、それだけ不良の拡散を防ぐことができるのだ。
「社内ではこれを製品の『トレーサビリティ』と呼んでいますが、その確立によって品質保証の精度をさらに高めたことは、非常に大きな前進でした」(石橋氏)
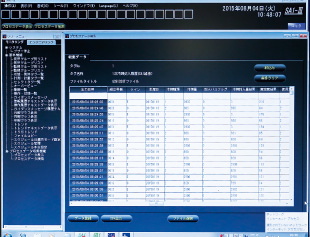
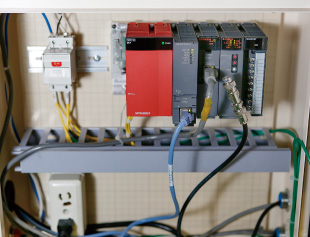
最適な生産計画に必要な現場情報をフィードバック。
SA1-Ⅲを製作所全体のシステム統合の土台に
RFIDシステムの導入にあたってなぜSA1-Ⅲだったのか?「現場のデータを収集するだけでなく、さらに上位の生産管理系のシステムにフィードバックする上で、SA1-Ⅲのフレキシブルさは魅力でした。実は、今回のシステム開発には、将来を見越した全体システム統合への布石という、もうひとつの目的がありました。それにはSA1-Ⅲが最適だと判断しました」(石橋氏)
60年の歴史をもつ同製作所には、さまざまな管理システムが混在している。資材管理や開発試験の管理システム、電源管理システムなどは既に先行してSA1を導入しているが、製造現場を管理するシステムはまだ旧システムのままバラバラに存在する。こうしたものを統合し、それぞれの情報の共有化と活用を進めていこうといのが、次なる構想だ。
そのメリットは計り知れない。最も期待されるのが、今回冷媒封入ラインで経験してきた「トレーサビリティ」であるという。例えば、さまざまな製造工程で実施されている検査情報を集約化できれば、製品そのものの品質保証の精度は格段に向上する。
静岡製作所で生み出された多彩な製品群は、世界に送り出されている。また、同製作所はタイやイギリス、中国にある海外7拠点を統括するマザー工場として、海外マーケット向け製品の開発・設計も行っている。ここで磨かれた生産システムもまた、海外拠点に展開される予定だ。その挑戦は、世界市場を展望したグローバルトップへの飛躍に繋がっている。

三菱電機株式会社 静岡製作所 | ● 設立:1954年 ● 事業内容:冷蔵庫、ルームエアコン、ハウジングエアコン、 事務所・店舗用エアコン、空調用コンプレッサー ● URL:http://www.mitsubishielectric.co.jp/ |